Оценка технологической эффективности переработки зерна (часть 1)
Рациональная организация контроля и управления технологическим процессом должна обеспечить высокую эффективность переработки зерна. Особенность мукомольного и крупяного производства состоит в том, что в общей структуре затрат на единицу массы готовой продукции затраты на зерно составляют от 94 до 96%. В связи с этим при практической организации и ведении технологического процесса необходимо обеспечить максимальный выход готовой продукции высшего качества.
Однако оценка эффективности переработки зерна только по выходу и зольности муки не позволяет сравнивать результаты производственной деятельности различных мукомольных заводов, перерабатывающих зерно разного качества. Существует несколько косвенных методов, позволяющих оценить технологическую эффективность. Одним из них является метод построения кумулятивной кривой зольности муки, представляющей собой зависимость средневзвешенной зольности муки от ее выхода, рассчитанной на основании данных баланса помола или же баланса муки:
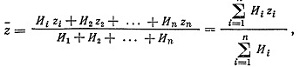
где Иi — извлечение муки на данной системе технологического процесса, % к I драной системе; zi — зольность данного потока муки, при этом i=1, 2,..., n.
Анализируя эту кривую, можно установить возможный выход муки по сортам и разработать конкретную компоновку потоков муки для формирования высшего, первого и второго сортов.
Исходные данные для расчета кумулятивной кривой получают, определяя извлечение муки по системам и ее зольность, т. е. снимая баланс муки. Для этого с каждой системы технологического процесса отбирают в течение строго определенного промежутка времени муку, чтобы в дальнейшем рассчитать ее извлечение по отношению к I драной системе и определить ее зольность. Можно также воспользоваться данными баланса помола, для получения которого отбирают в течение точно известного промежутка времени все продукты со всех систем технологического процесса.
На рисунке ХХIХ-3 показаны кумулятивные кривые зольности муки. Кривая 3 расположена заметно ниже кривой 1; разница в зольности муки составляет 0,16...0,22% при одном и том же извлечении. Это результат высокого уровня организации и ведения технологического процесса на мукомольном заводе.
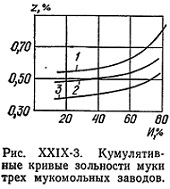
- Организация и контроль автоматизированного управления (часть 6)
- Организация и контроль автоматизированного управления (часть 5)
- Организация и контроль автоматизированного управления (часть 4)
- Организация и контроль автоматизированного управления (часть 3)
- Организация и контроль автоматизированного управления (часть 2)
- Организация и контроль автоматизированного управления (часть 1)
- Контроль и управление основными технологическими процессами
- Особенности производства комбикормов за рубежом (часть 2)
- Особенности производства комбикормов за рубежом (часть 1)
- Схемы заводов. Выход и показатели качества комбикормов (часть 2)
- Схемы заводов. Выход и показатели качества комбикормов (часть 1)
- Производство премиксов
- Особенности производства белково-витаминных добавок (БВД)
- Производство карбамидного концентрата
- Производство крупки из гранул и повышение их водостойкости
- Производство гранулированных комбикормов
- Принципиальная схема производства комбикормов и БВД
- Линии дозирования и смешивания компонентов
- Ввод мелассы и другие способы ввода жидких компонентов (часть 2)
- Ввод мелассы и другие способы ввода жидких компонентов (часть 1)
- Линия подготовки жидких компонентов
- Линия подготовки премиксов
- Линия отделения пленок у овса и ячменя. Другие линии (часть 2)
- Линия отделения пленок у овса и ячменя. Другие линии (часть 1)
- Линия прессованного сырья. Подготовка соли и мела
- Линии мучнистого сырья. Кормовые продукты пищевых производств
- Подготовительные линии сырья - Линия зернового сырья (часть 2)
- Подготовительные линии сырья - Линия зернового сырья (часть 1)
- Процесс производства комбикормов, БВД и премиксов
- Рецептура комбикормов. Применение ЭВМ для расчета (часть 2)