Использование побочных продуктов (часть 4)
На рисунке XVII-1 приведена одна из простых технологических схем получения пшеничного зародышевого продукта на мукомольном заводе.
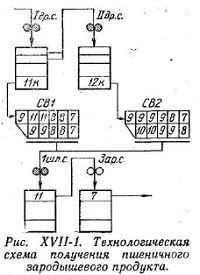
По данной схеме крупная крупка с I и II драных систем, обогащенная в ситовеечных машинах, поступает на 1-ю шлифовочную систему, верхний сход с которой направляется на зародышевую систему. Здесь на валках с микрошероховатой поверхностью (отношение окружных скоростей 1:1) он плющится и затем выделяется верхним сходом с рассева.
По этой или подобной схеме можно получить около 0,3% зародышевого продукта от массы переработанного зерна. Чистота его заметно снижается при повышении выхода.
Так, в эксперименте установили, что при выходе 0,1% чистота зародышевого продукта составляла около 90%, при выходе 0,3% — 75%.
При переработке риса зародыш выделить труднее. Однако имеются сообщения, что в Индии разработан дежерминатор специальной конструкции. Применение этого дежерминатора позволяет выделить около 90% зародыша.
Зародыш кукурузы достаточно легко отделяется от зерна в дежерминаторах, а также в зародышеотделительных машинах. Конструктивно они подобны обоечным машинам. Для выделения зародыша из продуктов дробления необходимо использовать пневмосортировальные столы.
Недостаток мучки заключается в том, что она быстро слеживается в силосе и ее трудно выгрузить из него. Чтобы устранить подобное явление, мучку следует гранулировать.
На ряде предприятий ее гранулируют в обычных прессах-грануляторах.
Отруби и лузгу также желательно гранулировать или прессовать. В результате улучшаются их физико-химические свойства и снижаются транспортные расходы.
При загрузке лузги и отрубей в железнодорожные вагоны в рассыпном виде вместимость вагонов используется всего на 25...35%. После гранулирования удается почти полностью использовать паспортную грузоподъемность вагонов.
Отруби также можно гранулировать в обычном оборудовании с применением прессов-грануляторов. При этом натура отрубей повышается от 350...400 до 630...650 г/л. Процесс гранулирования отрубей проходит эффективно при использовании воды, пара или связующих веществ.
Труднее поддается брикетированию рисовая лузга. Для формирования прочных брикетов нужно очень высокое давление (140...200 МПа) при условии предварительной обработки лузги паром и нагреве ее до температуры 70...80°С. Плотность полученных брикетов достигает 900 кг/м3, насыпная плотность — 720 кг/м3. Но процесс требует большого расхода энергии и специальных мощных прессов, что сдерживает его реализацию.
Побочные продукты мукомольного и крупяного производства используют еще недостаточно эффективно. Необходимо разработать технологию получения на их основе витаминов, фитина, белка и других ценных продуктов.
Это один из определяющих факторов разработки безотходной технологии муки и крупы.
- Использование побочных продуктов (часть 3)
- Использование побочных продуктов (часть 2)
- Использование побочных продуктов (часть 1)
- Производство специальных видов муки (часть 4)
- Производство специальных видов муки (часть 3)
- Производство специальных видов муки (часть 2)
- Производство специальных видов муки (часть 1)
- Формирование потребительских достоинств муки и крупы (часть 6)
- Формирование потребительских достоинств муки и крупы (часть 5)
- Формирование потребительских достоинств муки и крупы (часть 4)
- Формирование потребительских достоинств муки и крупы (часть 3)
- Формирование потребительских достоинств муки и крупы (часть 2)
- Формирование потребительских достоинств муки и крупы (часть 1)
- Потребительские достоинства и ценность муки и крупы (часть 2)
- Потребительские достоинства и ценность муки и крупы (часть 1)
- Оптимизация и стабилизация технологических свойств (часть 7)
- Оптимизация и стабилизация технологических свойств (часть 6)
- Оптимизация и стабилизация технологических свойств (часть 5)
- Оптимизация и стабилизация технологических свойств (часть 4)
- Оптимизация и стабилизация технологических свойств (часть 3)
- Оптимизация и стабилизация технологических свойств (часть 2)
- Оптимизация и стабилизация технологических свойств (часть 1)
- Упрощенный метод технологической эффективности (часть 2)
- Упрощенный метод технологической эффективности (часть 1)
- Прямой метод технологической эффективности (часть 2)
- Прямой метод технологической эффективности (часть 1)
- Оценка содержания крахмала в зерне (часть 2)
- Оценка содержания крахмала в зерне (часть 1)
- Оценка по зольности. Оценка на основе баланса муки (часть 3)
- Оценка по зольности. Оценка на основе баланса муки (часть 2)